15. April 2024 von Dr. Patrick Kübler
Warum unsere Kunden beim Thema IIoT mit einem Produktionsreporting beginnen
Tagtäglich erleben wir bei unseren Kunden, dass Mitarbeitende Berichte manuell erstellen müssen. Dabei müssen sie Daten aus verschiedenen Systemen und von vielen Ansprechpersonen im Unternehmen zusammentragen. Die Kennzahlen werden dann in mehreren Schleifen von verschiedenen Beteiligten geprüft, überarbeitet und freigegeben.
Negative Auswirkungen des manuellen Reportings
- Der manuelle Reportingprozess verursacht hohe Personalkosten.
- Gut ausgebildete Mitarbeitende können ihre Fähigkeiten nicht zur Prozessoptimierung einsetzen, sondern sind in stark repetitiven Aufgaben gefangen.
- Es wird immer schwieriger, Mitarbeiterinnen und Mitarbeiter zu finden, die diese Aufgaben übernehmen wollen.
- Die generierten Kennzahlen sind nie aktuell und ermöglichen keine zielgerichtete Steuerung der Produktion.
- Berichte durchlaufen oft mehrere Überarbeitungsschleifen, um politische Aspekte zu berücksichtigen, was die Qualität der Kennzahlen mindert.
- Aufgrund des repetitiven Charakters der Arbeit kommt es häufig zu Fehlern bei der Datenerfassung und der Berechnung der Kennzahlen, was die Qualität der Kennzahlen weiter mindert.
Hohe Bedeutung des Reportings
All dies steht in krassem Gegensatz zur Bedeutung von Kennzahlen für Führungskräfte, da die Produktion seit jeher stark effizienz- und damit kennzahlengetrieben ist. Meist hängt die Vergütung der Führungskräfte von der Erreichung vorgegebener Ziele ab - wie etwa der Senkung der Herstellkosten, der Reduzierung der Ausschusskosten, der Erhöhung der Liefertreue oder der Steigerung der Anlagenverfügbarkeit. Das Interesse an aussagekräftigen und qualitativ hochwertigen Kennzahlen ist daher durchweg hoch.
Warum unsere Kunden mit der Automatisierung des Reportings starten
Wir sehen bei unseren Kunden eine stark wachsende Bedeutung der Themen IIoT und Digitalisierung der Produktion. Kein Unternehmen kann es sich heute noch leisten, hier nicht aktiv zu sein. Aber warum fangen viele Unternehmen ausgerechnet beim Reporting an?
Neben der bereits erwähnten hohen Bedeutung von Reportings gibt es folgende Gründe:
- Berichte haben eine hohe Aufmerksamkeit auf Managementebene und bilden die Grundlage für wichtige Unternehmensentscheidungen, auch für Investitionen in die Digitalisierung.
- Aus technischer Sicht ist das Reporting von Kennzahlen vergleichsweise einfach, da keine Echtzeitanforderungen bestehen und nicht direkt in laufende Prozesse eingegriffen werden muss.
- Der Business Case ist einfacher zu kalkulieren, da der wegfallende manuelle Aufwand, der in der Regel durch das Reporting entsteht, gut abschätzbar ist.
Was ist so besonders an der Produktion?
Die meisten unserer Kunden verfügen bereits über ein automatisiertes Reporting in anderen Fachbereichen. Im Gegensatz zur Produktion liegen die Daten dort jedoch zentral in einem führenden IT-System vor. Ganz anders sieht es in der Produktion aus. Dort sind nicht selten Dutzende von Shopfloor-Applikationen allein in einem Werk im Einsatz. Entsprechend verteilt liegen die Daten in unterschiedlichen Systemen vor. Teilweise müssen die Daten erst aus den Maschinensteuerungen gesammelt werden. Das bedeutet, dass der Aufwand weniger in der Visualisierung von Kennzahlen liegt, sondern vielmehr in der automatisierten Datenerfassung durch die Integration unterschiedlicher Produktionssoftwaresysteme.
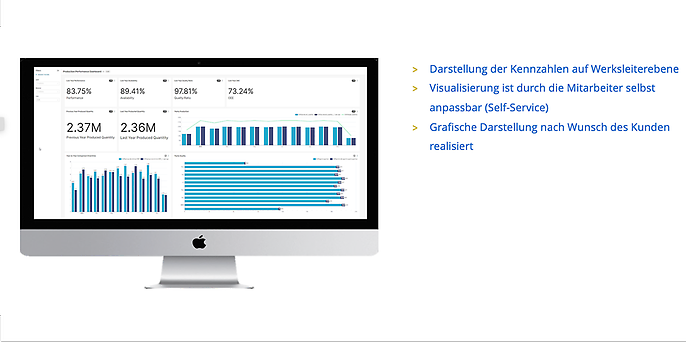
Abbildung 1: Das Projektvorgehen zum Produktionsreporting bei adesso
Wie gehen wir im Projekt vor?
Abbildung 1 fasst unser Projektvorgehen in diesem Zusammenhang zusammen. Zu Beginn des Projektes gehen wir in die Produktion und verschaffen uns einen ersten Überblick. Um das Rad nicht neu zu erfinden, analysieren wir bestehende (meist Excel-basierte) Steuerungslösungen und erfassen die Datenquellsysteme. Wichtig in dieser Phase ist die enge Einbindung der verschiedenen Stakeholder. Auf Basis dieser Analysen erstellen wir ein Fachkonzept und visualisieren dieses möglichst früh im Projekt mit Hilfe von Mockups oder Wireframes. Diese grafischen Darstellungen erleichtern uns die Diskussion mit den Stakeholdern und helfen, das Fachkonzept im Rahmen eines Workshops zu finalisieren. Danach folgt der aufwändigste Teil des Projekts: Die Entwicklung von Schnittstellen zu den Quellsystemen, um an die entsprechenden Daten zu gelangen. Nach der eigentlichen Implementierung folgt die Inbetriebnahme inklusive Schulung der Key-User.
Was sind wichtige Erfolgsfaktoren bei der Umsetzung?
Unsere Erfahrung zeigt, dass Reportingprojekte nicht rein technisch betrachtet werden dürfen. Denn Reporting und Kennzahlen sind oft emotional aufgeladene Themen, da sie direkten Einfluss auf die Gehälter der Führungskräfte haben. Deshalb unterstützen wir unsere Kunden neben der technischen Realisierung auch bei der fachlichen Ausgestaltung des Reportings und bei der Einführung im Rahmen eines professionellen Change Managements.
Zu Projektbeginn bringen wir ein Standardkennzahlensystem und ein Dashboard mit, das auf Best Practices aus anderen Kundenkontexten basiert. In den meisten Fällen passen wir die Vorlage im Laufe des Projekts an die Unternehmensziele und das spezifische Produktionssystem an. Dabei ist es wichtig, die Kennzahlen standortübergreifend einheitlich zu berechnen und die relevanten Quellsysteme für die Datenbeschaffung zu identifizieren. Früh im Projekt werden Mock-ups entwickelt, um die Benutzerfreundlichkeit sicherzustellen und das Engagement aller Beteiligten zu gewinnen. In einigen Fällen ist es sinnvoll, der Produktion bereits ein Dashboard zur Verfügung zu stellen, das zunächst manuell oder über einen Excel-Import mit Daten befüllt werden kann. So haben die Verantwortlichen frühzeitig etwas in der Hand und sehen den Mehrwert des Projektes. Wichtig ist, dass diese Dashboards auch später in der automatisierten Umgebung genutzt werden können, um nicht unnötigen Mehraufwand zu erzeugen.
Welche Technologien setzen wir in den Projekten ein?
Da die meisten unserer Kunden zunächst in anderen Fachbereichen mit der Automatisierung des Berichtswesens beginnen, sind häufig bereits BI-Lösungen im Einsatz. Typische Technologien sind beispielsweise SAP BW oder Snowflake als Data Warehouse und PowerBI, SAP SAC oder Tableau als BI-Lösung. Um kein weiteres Silo zu schaffen und die Komplexität für das IT-Management nicht weiter zu erhöhen, sollten die bereits im Einsatz befindlichen Technologien auch in der Produktion genutzt werden.
Vor allem bei den Quellsystemen treffen wir auf eine sehr hohe Heterogenität. So sehen wir in unseren Projekten unterschiedliche MES-Systeme wie MPDV Hydra, SAP DM, Felios oder Critical Manufacturing MES. Je näher man an die Feldebene kommt, desto heterogener werden die Systeme - vor allem im internationalen Kontext. Während wir in Deutschland häufig mit Siemens-Steuerungen zu tun haben, kann es sein, dass wir beim gleichen Kunden in den amerikanischen Werken beispielsweise mit Rockwell-Steuerungen arbeiten. Hinzu kommt als weiterer Komplexitätstreiber das unterschiedliche Alter der verbauten Steuerungen.
Aber nicht nur die eingesetzte Hardware ist vielfältig, wir haben es auch immer wieder mit sehr heterogenen Datenmodellen der Anlagen zu tun. Nicht selten muss für jede Anlage eine eigene Lösung erarbeitet werden. Hier empfehlen wir unseren Kunden „so nah wie möglich“ an der Maschine zu standardisieren und nicht zu versuchen, das Problem in übergeordneten Softwaresystemen zu lösen. Das bedeutet, dass zu Projektbeginn ein einheitliches Datenmodell für gleichartige Anlagen definiert und implementiert werden muss, damit die Daten in den übergeordneten IT-Systemen verarbeitet werden können.
Auf was legen unsere Kunden wert?
Unsere Kunden legen Wert darauf, dass die Lösungen skalierbar sind, die Kennzahlen einheitlich berechnet werden und die Dashboards je nach Unternehmensebene unterschiedliche Informationsinhalte anzeigen. Denn ein Schichtleiter benötigt andere Informationen als ein Vorstand, um seine Aufgaben effizient erledigen zu können. Viele Kunden wollen die Dashboards selbst individuell anpassen können. Berechtigungskonzepte stellen dabei sicher, dass nicht jeder alles sieht und die Darstellungen nur von den berechtigten Mitarbeitern angepasst werden können. Um die gewonnenen Daten auch für weitere Digitalisierungs-Use-Cases nutzen zu können, ist es wichtig, keine separaten Datensilos zu schaffen, sondern die Daten in einer zentralen Plattform zusammenzuführen.
Ohne Datenqualität geht nichts!
Wie immer bei der Digitalisierung spielt die Datenqualität eine zentrale Rolle für die Aussagekraft der Kennzahlen. Die Verantwortung für die Datenqualität muss im Fachbereich liegen. Die besten Erfahrungen haben wir gemacht, wenn die Verantwortlichkeit klar geregelt und ein Data Steward im Fachbereich benannt wurde.
Abbildung 2 zeigt ein beispielhaftes Dashboard aus Sicht eines Werksleiters, das wir für einen Kunden entwickelt haben.
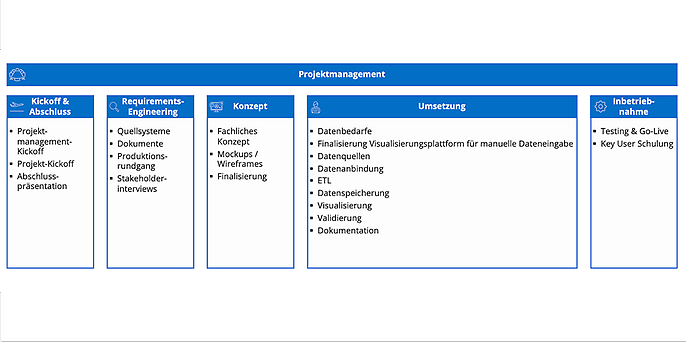
Abbildung 2: Beispiel für eine Realisierung
Weitere Vorteile eines Produktionsreportings für unsere Kunden
Die automatisch generierten Kennzahlen schaffen Transparenz über den aktuellen Stand der Produktion, was die Identifikation von Handlungsfeldern und damit die gezielte Investition in Digitalisierungsprojekte erleichtert. Aktuelle Kennzahlen erleichtern die Bewertung des wirtschaftlichen Mehrwerts vieler Digitalisierungsprojekte in der Produktion. Die Dashboards schaffen zudem Sichtbarkeit für das Thema Digitalisierung bei Führungskräften und Mitarbeitern, was die Bereitschaft für weitere Projekte erhöht.
Wie geht es dann weiter?
Im Rahmen des Berichtsprojekts werden bereits Datenmodelle und Architekturen entwickelt, um Daten von der Feldebene bis zur Unternehmensleitebene verarbeiten zu können. Also genau das, was unter dem Schlagwort „IIoT“ verstanden wird. Wir empfehlen unseren Kunden daher, bereits im Reporting-Projekt die weiteren Schritte auf der Digitalisierungsroadmap zu antizipieren und entsprechende Konzepte und Architekturen zu entwickeln, die den weiteren Ausbau unterstützen.
Kostenloses Whitepaper: Wie Unternehmen mit IIoT-Plattformen nachhaltige Optimierungspotenziale identifizieren können
Eine IIoT-Plattform einzuführen ist aufwändig. Die falsche Plattformlösung führt schnell zu Frust und wird nicht genutzt. Damit das Einführen einer IIoT-Plattform zu einem Erfolg wird, ist eine gute Vorbereitung wichtig. Dabei hilft euch dieses Whitepaper.
Weitere spannende Themen aus der adesso-Welt findet ihr in unseren bisher erschienenen Blog-Beiträgen.