10. October 2022 By Fernando Arévalo and Dr. Uwe Pohlmann
A Preamble for Machine Data Collection on the Shop Floor
Finding patterns in data is a task that keeps data scientists and domain experts busy. Industrial companies are interested in this because discovering patterns can lead to process optimisation (e.g. finding the best process recipe or set of process parameters), finding the causes of anomalies, material forecasting for supply management, and predicting energy consumption. Data, then, is a crucial business asset that can add value. A first milestone is the collection of machine data. For this purpose, shop floor connectivity plays an essential role by making machine data accessible. Thus, the data can be stored, engineered, analysed, and modelled. Finally, the results of data analysis and modelling can be used to optimise the process and add a competitive advantage to the company.
An Example
The plant manager has come back from the last industrial convention. And guess what? The manager saw a neat demonstration of how to collect machine data on one of the stands. And the convention demonstration? Usually a (very) simple use case with a programmable logic controller (PLC), some sensors, and a nice dashboard to show variables, trends, and some indicators. The manager gathers his engineering team. The engineering team is doing outstanding work executing successful projects in the production halls. Typical tasks? Upgrading electrical infrastructure, installing new machine lines, replacing automation components. The manager requests a pilot project on one of the machines for the next quarter. Head of engineering scratches her head, still, it’s a nice change from the usual business and a chance to learn something new, right? The project is set.
The head of engineering gathers her team, and they start brainstorming right away. 3 to 4 months is tight, isn’t it? The team kicks off the project. All right, the cogs are turning. They come up with a plan and define the main milestones:
- Use case proposal (e.g. definition of goals, success metrics, budget, overall scope, milestones).
- Evaluation of machine connectivity (e.g. communication cards in the PLC and industrial PC (IPC)).
- A first architecture draft for the data collection (e.g. an ad-hoc backend for the data collection and a dashboard).
- Execution plan (e.g. Gantt chart, agile).
We will focus this time on the evaluation of machine connectivity. Be kind! The digitisation pie is a big one, so please take it one slice at a time. Let’s check the topic in detail.
Shop Floor Connectivity
The data realm belongs to two different worlds: on the one hand, we have the shop floor with all the machines and devices landscape. Where the data is. And on the other hand, we have the data sciences side. Where the data adds value to the business. All right! There is more to it. We have more parties such as the quality control system, enterprise resource planning (ERP), manufacturing execution system (MES) / distributed control system (DCS) / supervisory control and data acquisition (SCADA). As described above, the data scientists are looking for patterns in the data. The essential step is the acquisition of the raw data. Sometimes, it’s the CSV/XML file that the machine delivers or the polling interrogation to get a data point directly from the machine using a communication protocol. Though there is a long way to get to the data, the first milestone is to assure machine connectivity or shop floor connectivity. Some common challenges that are faced while performing this activity are:
- The machine has no communication card. As harsh as it sounds, this situation means that the machines are not accessible, and therefore, there is no chance of collecting data. This situation is not usually the case; however, it is still possible.
- There is no industrial network on the shop floor. Like the previous point, there is no chance of collecting data if the machines work as island systems. Therefore, the team needs to set up an industrial network on the shop floor.
- The communication protocol is not compatible with the data collection system. Popular industrial communication protocols for data collection are OPC-UA and MQTT. However, not all the machines are equipped with such protocols. The solution is a machine upgrade through a retrofit (e.g. gateway MODBUS-TCP to OPC-UA).
- The machine uses only a proprietary protocol. Yet the controller has digital inputs (DI) / digital outputs (DO). Still, the last resource is hardwiring the signals we want to obtain to a middle device (e.g. datalogger) that can communicate to the data collection system.
- The machine delivers only XML/CSV files. This situation implies a shared folder between the machine and the data collection system. This way, the data collection system can retrieve the file.
At this point, we have identified the usual challenges for shop floor connectivity. It seems like a lot of information to process, doesn’t it? What about an overview diagram to summarise the information? The diagram illustrates a typical setup for shop floor connectivity:
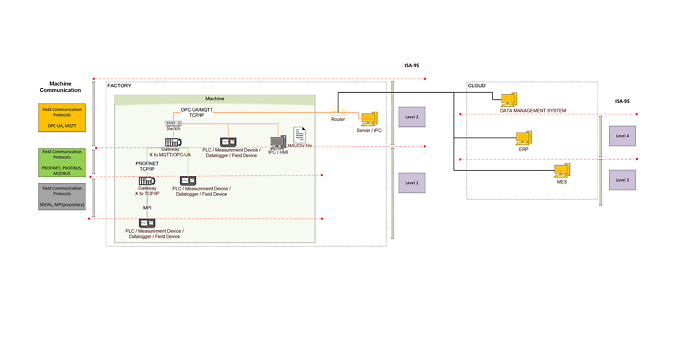
Architekturbeispiel für maschinelle Datenerfassung
There is a distinction between the machine communication levels on the left-hand side. On the right-hand side, the different levels of the automation pyramid are displayed according to the ISA-95.
So far, the team has evaluated the connectivity of the machines. At this point, the machines are accessible, and it is possible to retrieve the data. But wait, it feels like something is missing. Yes, which data? The team realises that plenty of variables are available from the machine (e.g. product number, the time required for production, machine downtime, and all the possible variables of the PLC). In addition, several systems generate data: machine, MES, energy management, quality control, and other devices (imaging systems for predictive maintenance, safety systems, sprinkler system).
Preliminaries for Machine Data Collection
When it comes to this task, it is crucial to consider the following points:
- Identify which machines or systems (e.g. MES, energy management) will be considered for the data collection system. The volume of data that a plant can generate cannot be underestimated.
- List of signals per data source and collection strategy (e.g. polling and/or event-based).
- Is there a need for data streaming?
- Definition of a data structure. Structured data eases data engineering, and posterior data analysis and modelling.
- Selection of data storage. Will the data be stored on-site, in the cloud, or a hybrid system?
- What if the desired signals do not exist? This situation requires extra engineering (e.g. signal identification, sensor selection, PLC-programming, datalogger).
- Finally, the different factory systems need to be accessible by the data collection system. The system interconnection plays a vital role in selecting the development platform for the data collection system.
Next Steps
We have checked the connectivity on the shop floor and looked at machine data collection. Further steps involve the design of the data management system, the evaluation of the interconnection of the different factory systems, considerations for the backend and frontend or the use of an established IoT platform, which type of data analysis will be performed, a strategy for predictive maintenance using data sciences, or even AI-models to assess the production.
Our experts for IoT/IIoT, smart products, digital production and data sciences are happy to support you in your projects. Would you like to learn more about IoT and our services in this area?
You can find more exciting topics from the adesso world in our blog posts published so far.